The PET sheet extrusion line procession: PET sheet, like other plastics, is closely related to molecular weight. The characteristic viscosity determines the molecular weight. The larger the typical thickness, the better the physical and chemical properties, but the fluidity is poor, making it difficult to mold. The lower the characteristic viscosity, its physical and chemical properties are poor, and the impact strength is lacking. Therefore, the typical thickness of the PET transparent sheet should be 0.8DL/g-0.9DL/g.
Taiz PET sheet extrusion line is storage device – stirrer – Ration feeder – extruder screw with planetary screws ( crystallizing and dying, exhaust water and gas ) – Filter Changer – melt metering pump – extrusion molding – calendering – cutting edge – traction – treatment -winding sheet.
1, storage device – stirrer – ration feeder: Raw materials or mix the raw material and the recycling PET slices materials. Ration feeder can control the feeding speed by PLA, can avoid material stacking at feeding hole.
2, single extruder screw with planetary-screw section: The PET material convert from the feeding hole to the planetary-screw section by heating and pressure. Our planetary-screw section is device with 9 small parallel screws, when the PET melt enter the device, the 9 small parallel screws will shear the PET melt fully, so the PET melt will release water and gas. Then our vacuum pump will suck and vent water and gas. That why our extruded PET sheet is higher transparency, better gloss, better toughness and more energy-efficient. So our single screw PET sheet extrusion line do not need crystallizing tower and dying tower to pretreat the PET raw materials. And also can do recycling PET materials.
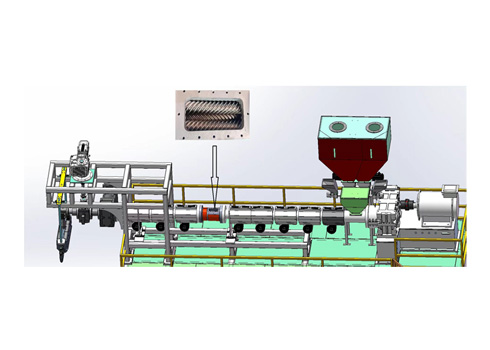
3, Filter changer – melt metering pump: Filter changer can change the filter net convinently by hydraulic system, ensure the impurities filtered fully. PLC controls the melt metering pump to control the extrusion volume.
4, extrusion molding: the PET melting polymer will be extruded to sheet with specific width by extrusion mould.
5, Calendering: Melt sheet from the mold directly to the three-roll calender, then calendering and cooling. PLA control the speed synchronization, ensure the speed is a little fast than the extrusion volume speed. So the three-roll calender can offset the expansion and weaken the internal stress of the sheet when the melt leaves the mold, and makes the wrinkles disappear.
6, cutting sheet edge – treatment ( oil coating, drying, corona, according to customers’ requirements) – traction -winding sheet (semi-automatic winder or fully automatic shaftless winder).