Plastic Sheet extruders are essential in the packaging industries for electronics, food, and pharmaceuticals. They heat and melt plastic raw materials, extruding them through molds to produce various packaging containers. With increasing quality demands and broader applications, it’s vital for operators to understand the machine’s features. Here’s an overview of their applications and maintenance.
Application Of A Plastic Sheet Extrusion Line:
Sheet extruders are primarily used for producing plastic sheets from materials like PET, PP, and PE. They melt and extrude plastics into sheets, which are then cooled and rolled. Common applications include food packaging, pharmaceuticals, electronics, and construction.
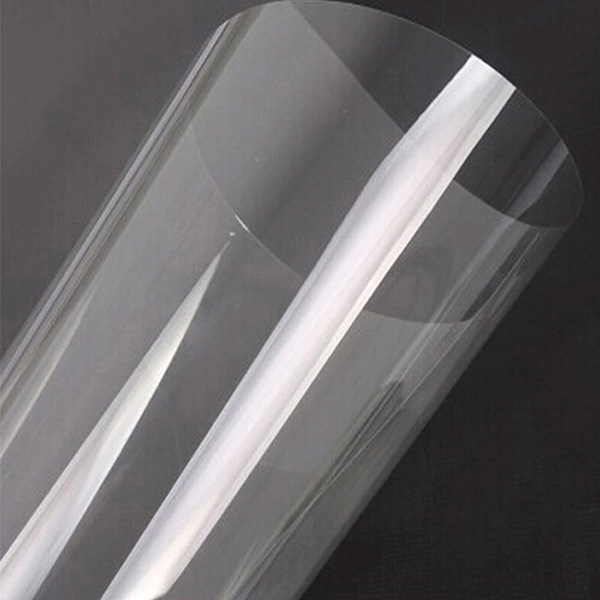
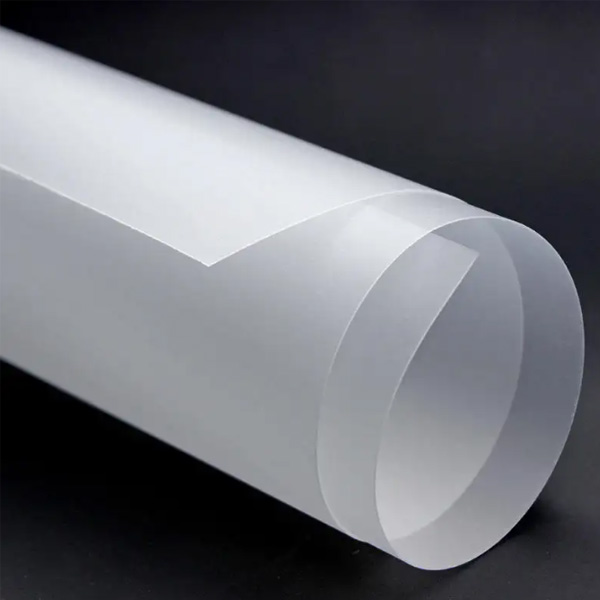
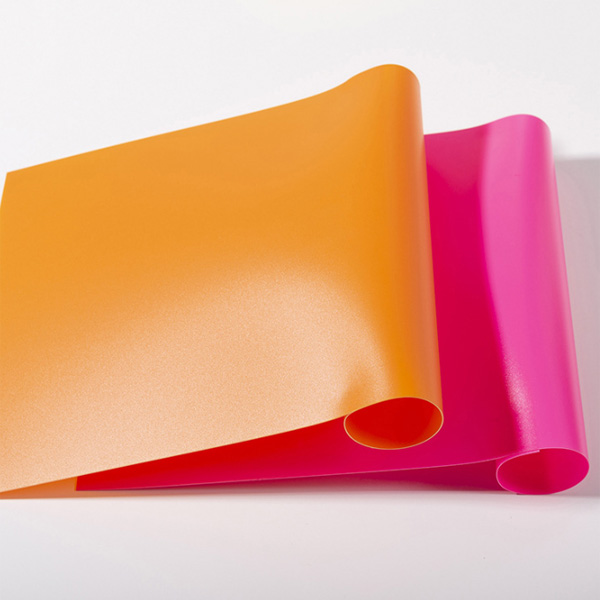
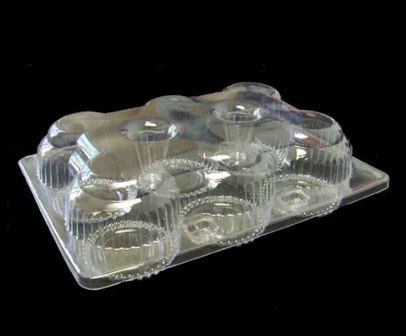
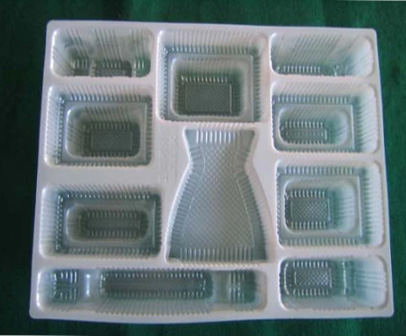
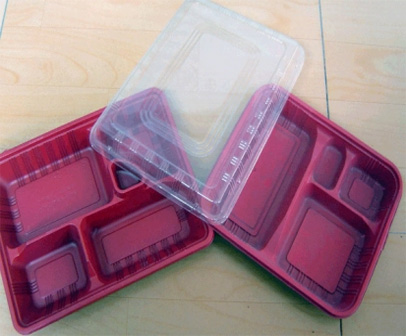
Maintenance Of A Plastic Extrusion Machine:
Regular maintenance is crucial for optimal operation and longevity of sheet extruders. Key maintenance tasks include:
Inspect Drive Components: Check gears, bearings, and belts for wear.
Check Hydraulic System: Inspect pumps, cylinders, and hoses for leaks.
Examine Electrical System: Ensure motors, cables, and panels function properly.
Clean Equipment: Maintain cleanliness and hygiene.
Inspect Molds: Check molds for wear and replace as necessary.
Lubricate Components: Ensure proper lubrication for smooth operation.
Control System Checks: Regularly inspect the control system for functionality.
Storage Precautions: Store unused equipment in a dry, ventilated area, with periodic checks.
In conclusion, effective maintenance of sheet extruders ensures reliable operation, extends lifespan, and enhances product quality. Operators should implement a regular maintenance schedule for best results.
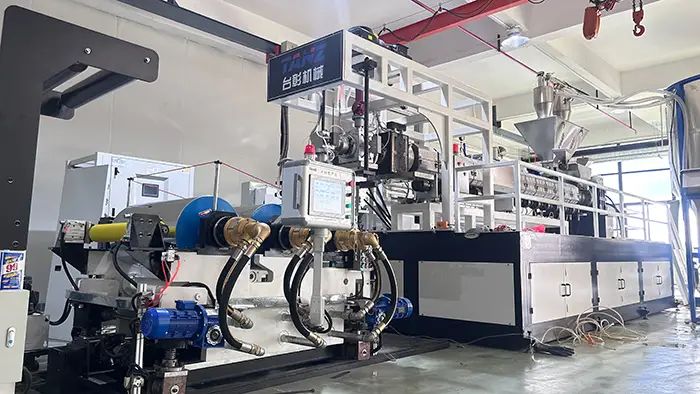