New Planetary Screw Technology In PET Sheet Production Lines
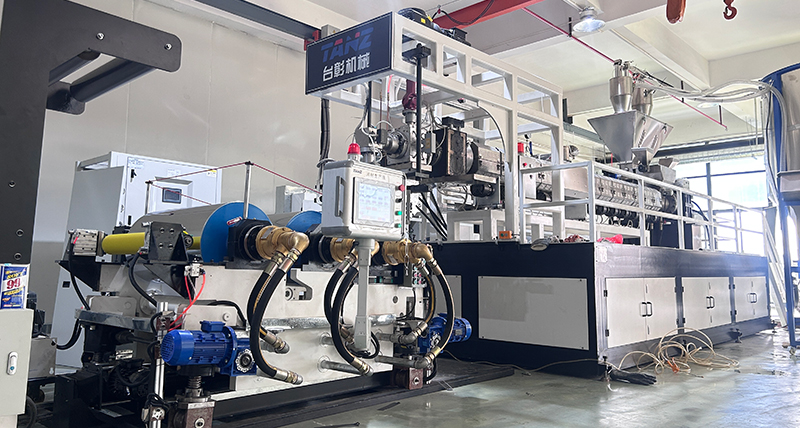
Core Principles of Planetary Screw Technology:
The planetary screw extruder features a central main screw surrounded by multiple planetary screws rotating synchronously. Through meshing transmission, the material undergoes repeated shearing, mixing, and stretching within the planetary section, creating an exceptionally large melt surface area (approximately 80× that of single-screw extruders and 30× that of twin-screw extruders). This enables two critical functions:
High-Efficiency Devolatilization: The expanded surface area, combined with a high-vacuum system (vacuum ≤10 Pa), rapidly removes moisture and volatiles. Raw materials with initial moisture content up to 0.8% can be processed directly, eliminating pre-crystallization or drying.
Enhanced Plasticization and Homogenization: The meshing motion of planetary screws improves material uniformity, enhances plasticization efficiency, and minimizes thermal degradation risks.
Key Advantages of Planetary Screw Technology:
Elimination of Pre-Drying and Crystallization
Traditional PET processing requires prolonged drying (≥4 hours at 160–180°C) to reduce moisture to <0.005%. Planetary screw systems bypass this step, cutting energy consumption by >30% while handling raw materials with ≤0.8% moisture.
Enables direct processing of 100% recycled PET (rPET) flakes, reducing preprocessing costs.
High Throughput and Energy Efficiency
Optimized cooling systems (e.g., thin-walled roller configurations) significantly boost production rates, surpassing conventional single/twin-screw extruders.
Reduced power consumption due to streamlined mechanical design and efficient energy utilization.
Material Versatility and Product Quality
Compatible with APET, PETG, rPET, and other polymers, supporting monolayer and multilayer sheet production.
Dual filtration (backwash + precision filters) ensures particle retention ≤200 μm, meeting FDA food-grade requirements.
Process Intelligence and Stability
Integrated programmable control systems and real-time viscosity monitoring enable dynamic parameter adjustments for consistent output quality.
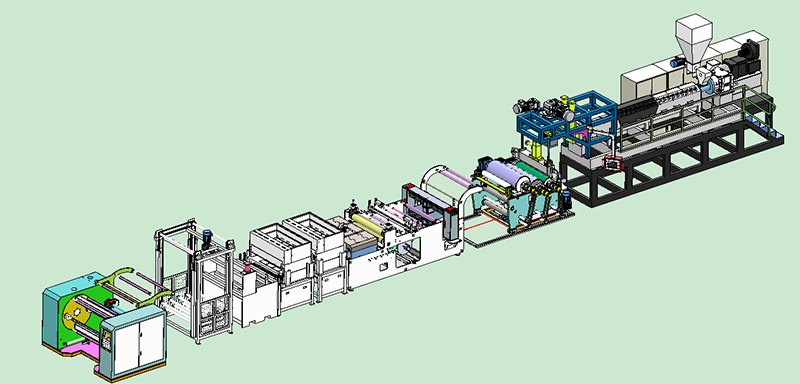
Process Flow of Planetary Screw-Based PET Sheet Lines:
Compared to conventional PET sheet production, planetary screw technology simplifies the workflow:
Traditional Process: Crystallization (30–90 min) → Drying (≥4 hr) → Extrusion → Calendering → Winding.
Planetary Screw Process: Direct feeding → Extrusion/plasticization (with synchronized devolatilization) → Calendering → Winding.
Eliminates pre-crystallization and drying stages, reducing cycle time by >50%.
Industrial Applications and Future Trends:
Key Applications
Food Packaging: Production of high-clarity, non-crystalline PET sheets compliant with food safety standards.
Recycled Material Processing: Direct utilization of 100% post-consumer rPET flakes, aligning with circular economy mandates.
High-Performance Products: Deep-drawn thermoformed items (e.g., 18 cm-depth cups), high-tensile strapping, and specialty films.
Emerging Trends
Integration with Chemical Recycling: Combining planetary screw systems with depolymerization technologies (e.g., glycolysis) to process diverse PET waste streams (e.g., fibers, films).
AI-Driven Optimization: Machine learning algorithms for screw geometry design, process parameter tuning, and predictive maintenance to maximize efficiency.
Conclusion
Planetary screw technology represents a paradigm shift in PET processing, addressing longstanding challenges in moisture removal and material homogenization. Its ability to bypass energy-intensive preprocessing steps while enhancing output quality positions it as a critical enabler for sustainable manufacturing, particularly in recycled PET and high-precision applications. Future advancements in chemical recycling and intelligent control systems are expected to further broaden its industrial relevance.
This document adheres to technical writing standards, emphasizing clarity, precision, and industry-specific terminology. For implementation guidance or detailed engineering specifications, consult OEM technical manuals or peer-reviewed publications.