With the development of the plastics industry, PP (Polypropylene) and PS (Polystyrene) sheets have gradually become market hotspots due to their excellent performance and wide range of applications. This article will explore the characteristics of PP and PS sheet extrusion production lines, their applications in the thermoforming product sector, the working principle, and common types of production lines.
Characteristics of PP and PS Sheet Extrusion Production Lines:
PP PS sheet extrusion production lines possess the following notable characteristics:
High Production Efficiency: The PP and PS extrusion lines utilize a continuous production process, enabling the rapid conversion of raw materials into finished products, thus meeting the demands of large-scale
Production Versatility: By adjusting processing parameters and mold design, production lines can manufacture sheets of varying thicknesses and widths, accommodating diverse market demands.
Excellent Processing Performance: PP and PS exhibit favorable flowability and thermoforming properties during the extrusion process, allowing them to maintain stable shapes and performance post-formation.
Environmental Friendliness and Safety: Both PP and PS materials are non-toxic and recyclable, aligning with the modern green production philosophy.
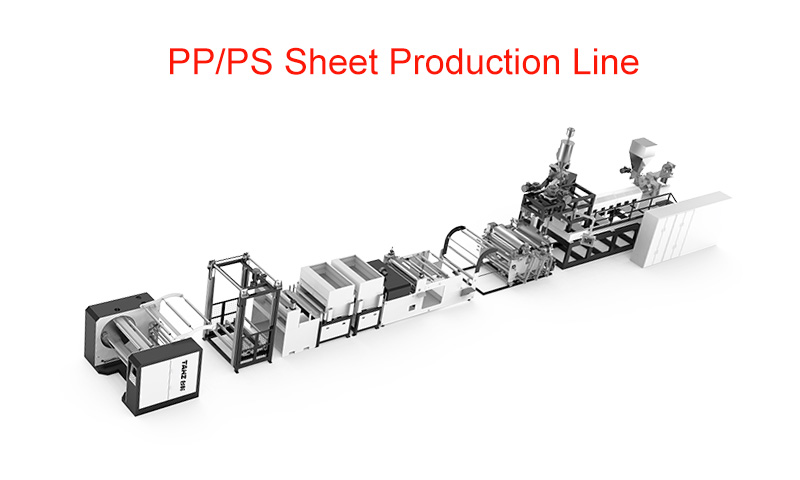
The Process of PP PS Extrusion Sheet:
The extrusion process for PP PS sheets primarily consists of the following steps:
Raw Material Feeding: PP or PS granules are fed into the extruder through a feeding system.
Plasticization and Homogenization: The screw rotates to heat and plasticize the raw materials, ensuring uniform distribution of the molten material.
Extrusion: The molten polymer is extruded through a die, forming sheets of the desired thickness and width. Variations in mold design lead to a variety of product forms.
Cooling: The extruded sheets pass through a three-roll calender, where they rapidly solidify and retain their shape.
Waste edge cutting and winding: when the PP PS sheet enter this device, the edge cutting circular knife will trim the sheet edge, and then a winding device will wind the waste edges on both side.
Silicone coating & drying: after waste edge trimming, the sheet go through silicone oil coating device to coat oil and two ovens to dry. the coated sheet is usually used for thermoforming products.
Winding to sheet roll: buffer rack + automatic winding machine, automatic to wind the sheet into roll for packaging. Automatically roll, automatically slit, automatically change sheet roll.
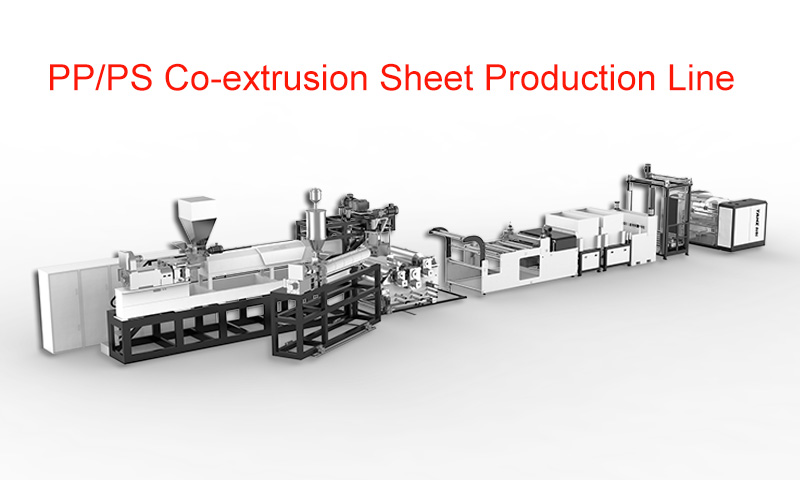
Common PP PS Sheet Production Lines:
The main types of PP and PS sheet extrusion production lines available in the market include:
Single Screw Extruder: This type of extruder is suitable for large-scale production, featuring simple operation and low maintenance costs, but is limited in its mixing capabilities for complex materials.
Twin Screw Extruder: This equipment provides superior mixing and plasticizing capabilities, making it suitable for high-performance products that require specific formulations, often used for co-extrusion of multiple materials.
Multi-layer Co-extrusion Production Line: Such lines are capable of simultaneously extruding multiple layers of materials, enhancing product performance and are commonly used for packaging and container products with high material performance requirements.
PP/PS Sheet Extrusion Production Line Solutions | |||
Extruder Qty | Single Extruder PP/PS Sheet Extrusion Line | Two Extruders PP/PS Co-extrusion Sheet Line | Multi Extruders PP/PS Co-extrusion Sheet Line |
Single layer sheet | Double-layer & three-layer sheet | Multi -layer sheet: five-layer, seven-layer or nine-layer | |
Extruder Type | Single screw & parallel twin-screw extruder | ||
Anchura de la hoja | 600-1220mm | ||
Thickness | 0.5-3.0mm | ||
Output | 2000kg/h-1000kg/h |
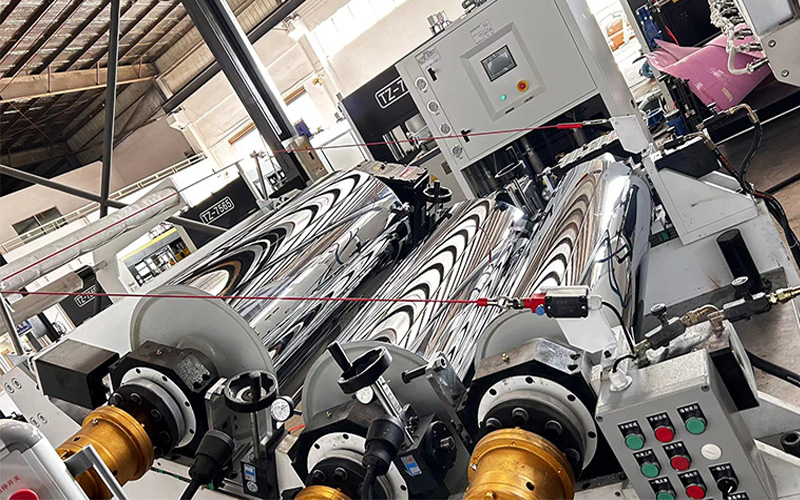